Exoskeletons from German Bionic successfully complete practical tests at DACHSER
- Exonr Technology
- Aug 11, 2022
- 4 min read
Updated: Nov 25, 2024
Following the successful completion of extensive tests, leading logistics specialist DACHSER is now putting our smart, fully connected exoskeletons into regular warehouse use. This involves, in particular, supporting various processes for unloading goods, picking, and other tasks requiring heavy lifting. The positive impact that the Cray X has on the health and safety of employees, together with its ease of use, was very convincing and ensured the swift acceptance by warehouse staff. In future, the new technology will also be implemented at other locations in the DACHSER network.
Exoskeletons pass practical trial: Innovative technology takes the strain for warehouse employees
For the first time, DACHSER has tested active exoskeletons produced by German Bionic under everyday work conditions in the warehouse. The results are impressive. Now the technology will be rolled out at additional locations.
Working in a warehouse still involves a lot of manual labor, and sometimes it can be physically demanding, too – for example when unloading goods or picking. DACHSER has long been looking into providing employees with technical aids to help them perform strenuous tasks. Exoskeletons hold particular promise. In medicine, external support structures of this kind have been in use for a long time; in industry, an increasing number of market-ready devices are now becoming available.
As early as 2019, DACHSER conducted initial warehouse tests, primarily of passive exoskeletons with mechanical spring systems, rails, or weights that assist in lifting loads. In the meantime, active exoskeletons have reached a level of maturity that can improve warehouse processes as well. Active exoskeletons use battery-powered robotic motors to facilitate lifting operations, greatly relieving strain on the lower back for anyone lifting heavier loads. Since wearers experience less fatigue, they are more able to maintain good posture.
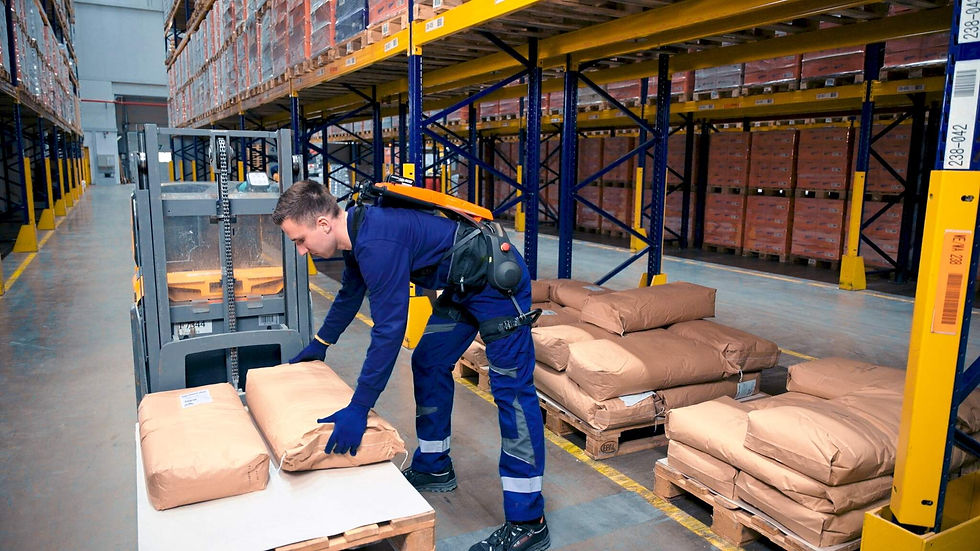
Active exoskeletons from German Bionic in use in Magdeburg
Active exoskeletons produced by the German manufacturer German Bionic were put through their paces in the warehouse at DACHSER’s Magdeburg logistics center in the spring. The aim was to gather empirical data under real conditions and to obtain feedback from employees. “Cray X” devices were deployed to support various processes in incoming goods, order picking, and at the packing table. The exoskeleton can provide 30 kilograms of relief per lifting operation and also assists with carrying.
The exoskeleton can provide 30* kilograms of relief per lifting operation and also assists with carrying.
“The positive effects of the exoskeletons soon became clear,” says Stephan Heinemann, Contract Logistics Manager at DACHSER’s Magdeburg logistics center. “Our employees benefit from direct relief when handling heavier loads as well as from ergonomic body stabilization. That has long-term advantages, too, since the exoskeletons prevent overexertion and workplace accidents that would be damaging to health.” Another impressive aspect of the devices was their ease of use, which meant that the testers accepted them in no time.
*This article is about the previous generation of German Bionic exoskeletons (Cray X), the new generation (Apogee) has 36kg (80lbs) of lifting compensation.
Technology with a future
This positive experience will be harnessed. “During testing, everyone noticed—as we had hoped they would—how the exoskeleton relieved their lower back, and rated this as positive,” Heinemann confirms. Accordingly, the location will make regular use of three active exoskeletons in the future.
Other locations in the DACHSER network will also use the new technology in their warehouses, including the Ulm logistics center starting in the fall. “By introducing new technologies and innovations, we’re continuously working to make DACHSER’s processes, including those in the warehouse, more efficient and effective. Above all, this includes providing support to people in all aspects of their warehouse activities,” adds Thomas Klare, Head of Corporate Contract Logistics at DACHSER. “Our use of active exoskeletons is an impressive demonstration of how modern technology not only makes work easier straight away, but can also have a positive impact on our logistics operatives’ long-term health.”
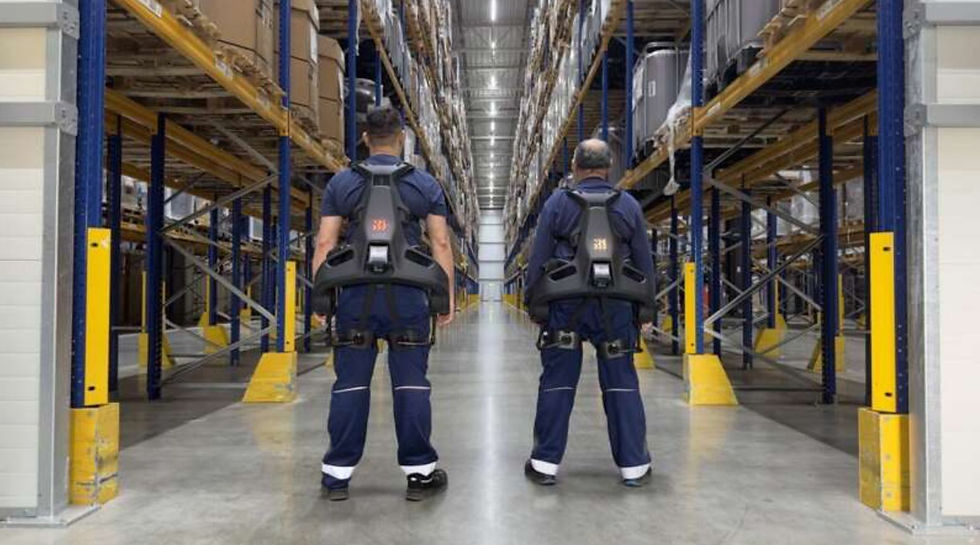
While amazing advancements continue to be made in automation, many operations in the logistics field still rely heavily on the flexibility and problem-solving skills of the workers on the shop floor – as well as their physical strength. To help avoid the threat of accidents and injuries that such constant physical strain can bring with it, work processes need to be optimized as much as possible and it is also vital that workers are properly trained and have ready access to equipment that can most effectively support them in their work and increase the levels of workplacesafety.
Logistics giant DACHSER has long recognized the importance of this. Indeed, Dachser was one of GermanBionic’s earliest customers. Since then, our e-exoskeletons have made their way into many of their warehouses and logistics operations.
Recently joining this ever-growing list is Dachser’s Hörsching site in the city of Linz, Austria. In a new article in Austria’s Tips media outlet, Michael Zoitl, Contract Logistics Manager at Dachser, talks about the deployment of the German Bionic Apogee power suits:
“Our ongoing commitment is to prevent overexertion and accidents. The exoskeletons enable employees to maintain safer lifting postures, enhancing their well-being.”
Our continuing partnership with Dachser and many other names in the industry not only underscores the role robotic exoskeletons are taking in the unbroken advancement of worker safety but also reflects the evolving standards within the logistics and warehousing industry as a whole.
Comments